The Game-Changing Impact of LSR Molding: Revolutionizing Product Design and Manufacturing
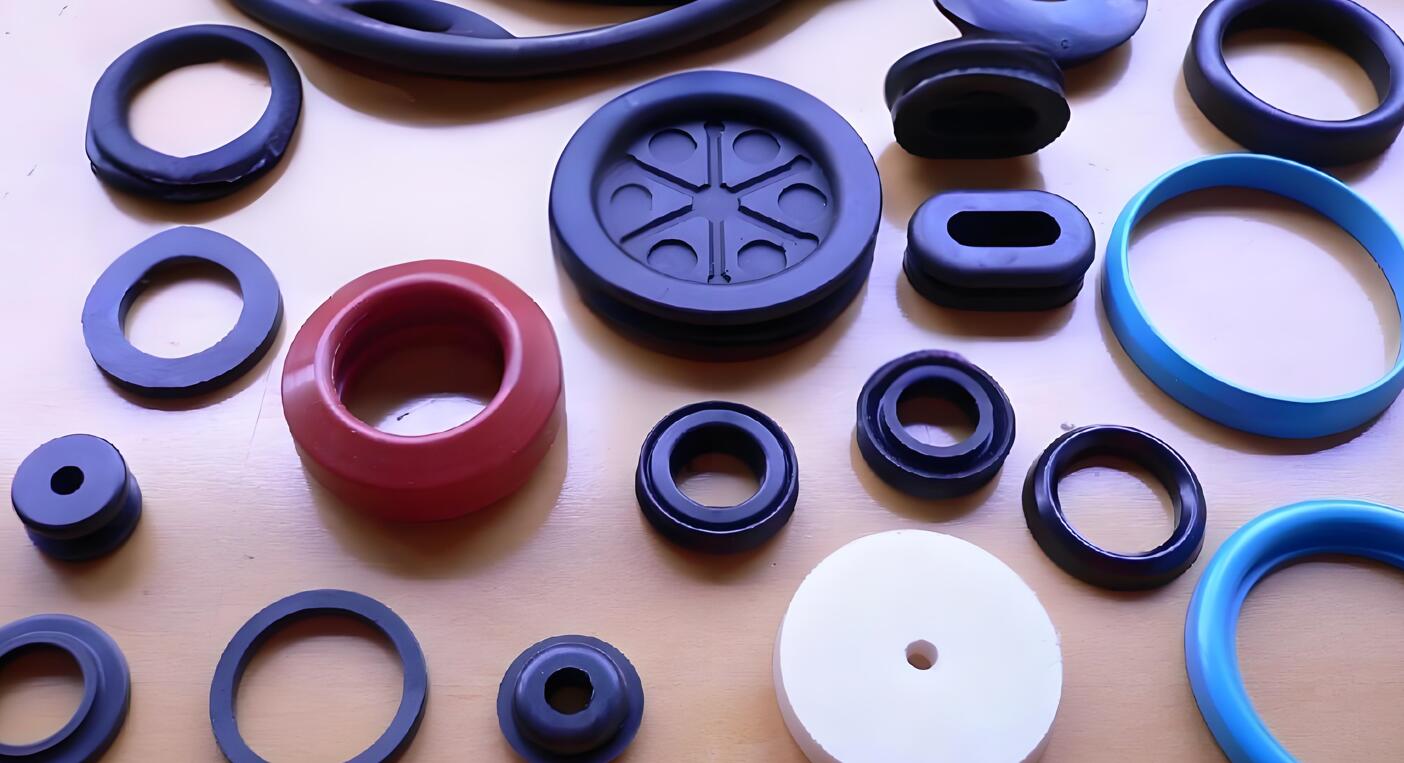
In the ever-evolving landscape of product manufacturing, a game-changing technology has emerged that is poised to revolutionize the industry. LSR injection molding is a cutting-edge process that combines the benefits of traditional injection molding with the versatility and efficiency of advanced techniques. This innovative approach to molding has the potential to unlock new possibilities for manufacturers, designers, and businesses across a wide range of industries.
Understanding the LSR Molding Process
At the heart of LSR molding lies a unique and streamlined approach to part production. The process begins with the insertion of a pre-formed component, such as a metal insert or a complex sub-assembly, into the mold cavity. This inserted component is then encapsulated by the injection of a molten polymer material, which conforms to the shape of the mold and the inserted component.
The key distinguishing feature of LSR molding is the subsequent stretching and releasing of the molded part. Once the polymer solidifies, you can open the mold and easily remove the finished product by stretching and releasing it. This stretching and releasing phase not only facilitates the extraction of the part but also enables the creation of intricate and precisely-engineered designs that would be challenging or impossible to achieve through traditional molding methods.
Advantages of LSRMolding
The adoption of LSR molding has ushered in a new era of product manufacturing, offering a multitude of advantages that set it apart from conventional molding techniques.
Increased Design Flexibility: It grants designers and engineers unprecedented freedom to explore complex geometries and intricate part designs. The ability to insert pre-formed components and the stretching and releasing process allows for the creation of parts with undercuts, internal cavities, and other advanced features that were previously difficult or impractical to produce.
Improved Efficiency and Cost-Effectiveness: The streamlined molding process reduces the number of production steps, ultimately leading to decreased cycle times and lower manufacturing costs. This increased efficiency translates to higher productivity and better profitability for businesses.
Enhanced Material Versatility: It is compatible with a wide range of materials, including thermoplastics, thermosets, and even advanced composite materials. This versatility enables manufacturers to select the most suitable materials for their specific product requirements, optimizing performance and durability.
Enhanced Part Integrity: The integration of pre-formed components and the precise control over the molding process in LSR molding result in parts with superior structural integrity and consistency. This leads to improved product quality, reliability, and long-term performance.
Reduced Environmental Impact: The streamlined molding process often requires less energy and generates less waste compared to traditional molding techniques. This environmentally-friendly approach aligns with the growing demand for sustainable manufacturing practices.
Real-World Applications of LSR Molding
The versatility of this techonology has allowed it to find applications across numerous industries, each benefiting from its unique capabilities.
Automotive Industry: Automakers often utilize LSR molding to produce complex components like door panels, dashboard inserts, and structural parts in the automotive industry. The ability to integrate metal inserts and achieve intricate designs has made LSR molding a preferred choice for automotive manufacturers.
Electronics and Consumer Goods: The electronics and consumer goods industries have embraced LSR molding for the creation of housings, enclosures, and other intricate components. The process enables the seamless integration of electronic components and the production of sleek, user-friendly designs.
Medical and Healthcare: The medical and healthcare sectors have particularly benefited from the advantages of LSR molding. This manufacturing process is suitable for producing medical devices, prosthetics, and other specialized products that demand high precision, durability, and biocompatibility.
Aerospace and Defense: The aerospace and defense industries have leveraged LSR molding for the production of structural components, sensors, and other mission-critical parts. The ability to incorporate advanced materials and achieve complex geometries has made LSR molding a valuable asset in these industries.
The Future of LSR Molding
As the manufacturing landscape continues to evolve, the importance of technology is only set to grow. With its demonstrated advantages and its ability to adapt to the changing needs of various industries, this innovative technology is poised to become a driving force in the future of product manufacturing.
Researchers and developers in the field of LSR molding are currently making progress in exploring new material combinations, integrating advanced sensors and automation, and optimizing production processes. Experts anticipate this technology will produce significant breakthroughs in the industry due to recent advancements. As these advancements unfold, the potential of this technology to transform the manufacturing industry will only continue to expand.
Conclusion
In the dynamic world of product manufacturing, LSR molding has emerged as a game-changer, offering a unique and powerful approach to part production. Combining the benefits of traditional injection molding with innovative stretching and releasing techniques has unlocked new possibilities for designers, engineers, and manufacturers across a wide range of industries.
As the adoption of LSR molding continues to grow, the future of product manufacturing looks brighter than ever, with the promise of increased efficiency, enhanced design flexibility, and a more sustainable industry. Embracing this revolutionary technology can unlock a world of opportunities for businesses and industries that seek to stay ahead of the curve.